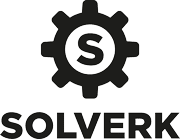
User friendly machine systems for adhesive application with one, two or three components built to increase your productivity
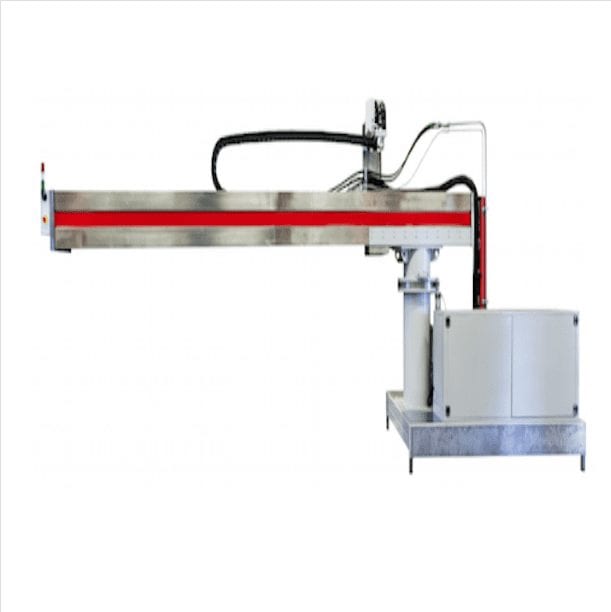
- Automatic
- 2 or 3 components
- PU, epoxy
- Large panels
- Moving spreader
Description
The M5 machine services a multiple of press/lay-up tables placed on either side of the machine track. The track can extend up to 100m to service a large set of tables. From the machine an arm extends out to the side above the press table. On the arm a trolley carries the adhesive spreader and moves it perpendicular to the track. The adhesive is applied through the spreader across the width of the panel.
The surface area can be programmed and stored as a recipe. The machine system will be designed and programmed to match your material flow, plant layout, products, selection of adhesive and environment.
The adhesive components are pumped through pipes and hoses laid down in an energy chain at the side of the machine track with the pump station positioned at the side of the production line. The pumps are of air driven piston type and the mixing ratio metering is done by mechanically linked measuring cylinders. The spreader is of steel and can be made at any width up to 600 mm.
When the work is complete the spreader is cleaned in a flush and cleaning station. For an one component adhesive system the spreader is automatically immersed and protected in an oil tray protecting the spreader from contact with the surrounding moisture in the air.
Operation
The operator programs the surface dimensions into the machines control system and then jogs the machine into starting position by guiding a laser marker. To simplify the operation the commands are performed using a hand held remote control. When in position the operator presses the start button and the machine applies the adhesive automatically on the surface area in accordance with the chosen programming and the operator can attend to preparing the next layer (or place the core material as the machine moves along the track). After the first adhesive layer is complete the process is mirrored by turning the direction switch.
When the work is complete the operator removes the spreader and mixer tube from the machine and clean them in the flush station. After reassembling the mixer and spreader onto the machine the system is ready for use again.
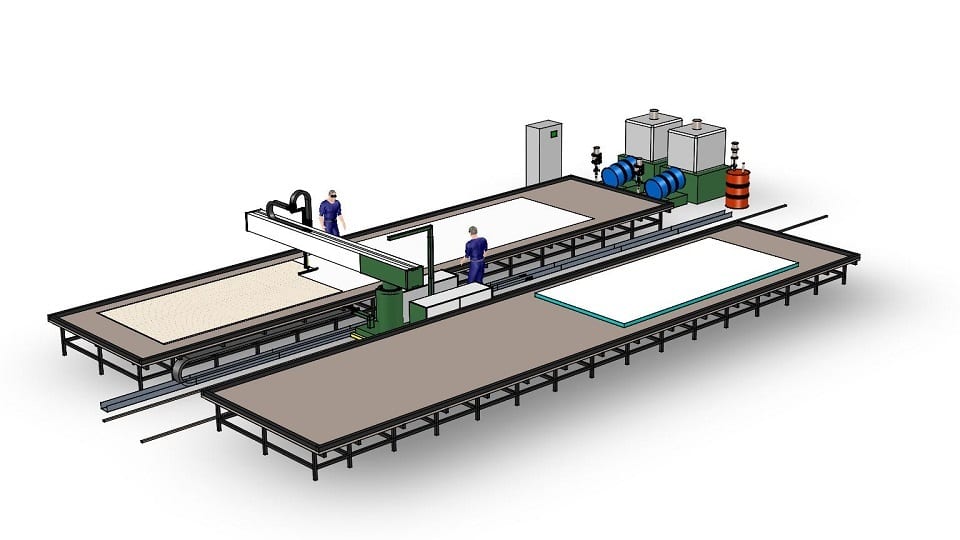
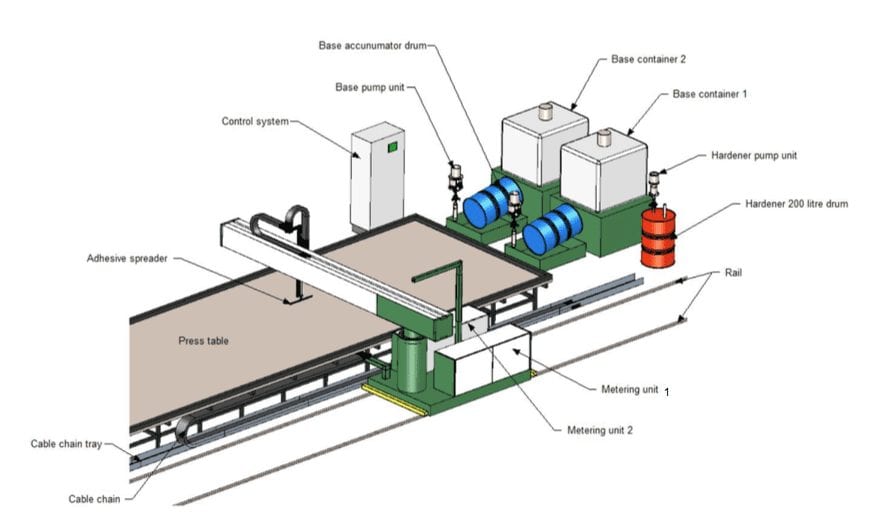
- Mixing ratio – 100:10 to 100:100 (fixed)
- Metering technique – Volumetric cylinder, mechanically linked
- Mixing technique – Static mixer
- Capacity – Up to 8kg/min
- Viscosity – Up to 100 000mPas
- System pressure maximum – 270 bar
- Track length – Up to 100m
- Machine dimensions LxWxH – 2.4 x 1.6 x 2.2
- Arm length – Customized (Max 7m)
- Net weight – 2500kg
- Power Electric – 400VAC, 3P, 50Hz, 16A
- Power pneumatic – 6B @ 1500l/min
Images
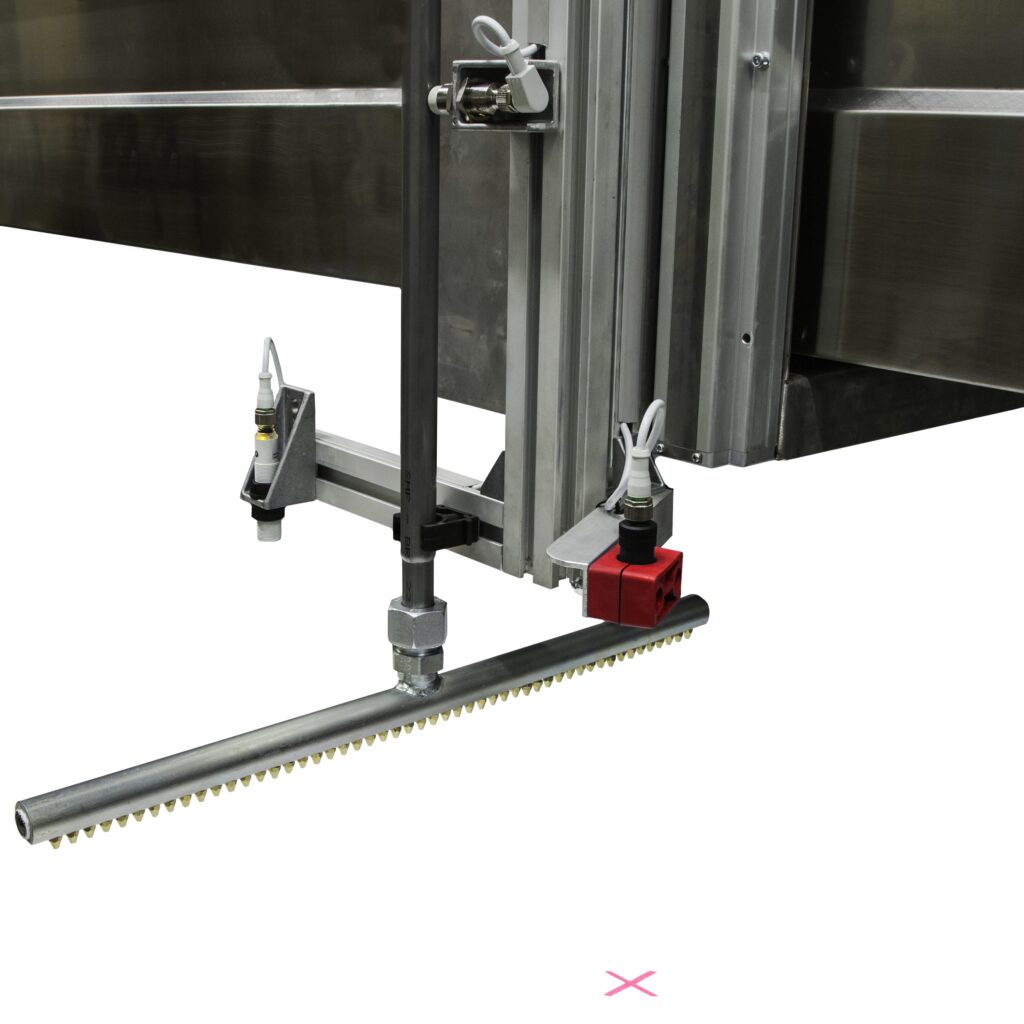
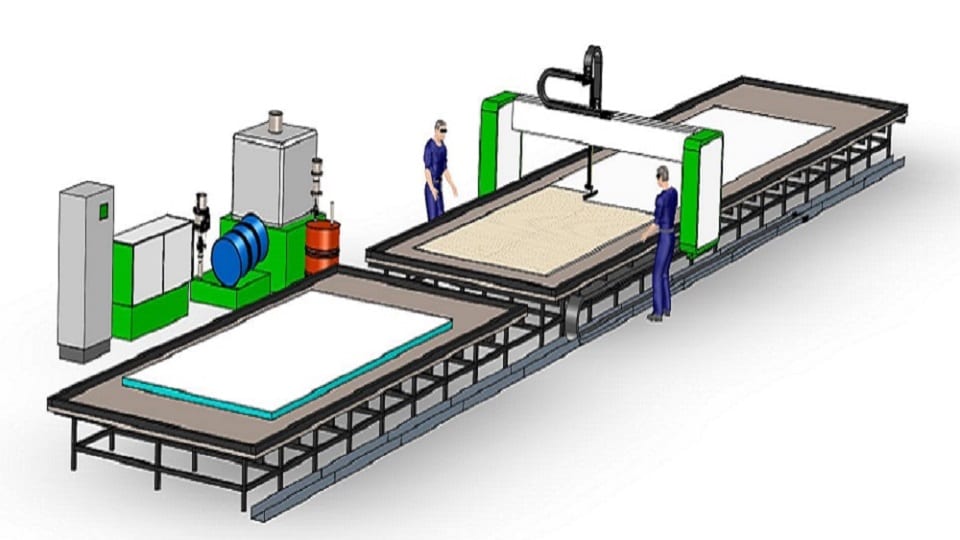
M4 – Auto
- Automatic
- 1, 2 or 3 components
- PU, Epoxy
- Medium-Large panels
- Fixed spreader unit
Basic info
Closely resembling the M5 but with a fixed spreader the M4 system is an automatic spreader system for one, two or three component adhesives.
The M4 system is an automatic spreader system for one, two or three component adhesives. The machine will automatically apply the adhesive over a programmed surface area meanwhile the operators prepare the next layer or inserts the insulation into the panel as the machine moves down the panel length. M4 is specifically designed for an efficient manufacturing of large sandwich panels and for the right customer the system will enable a substantial increase of productivity.
Description
The M4 machine can service up to two press/lay up tables placed after each other. Each table can extend to 20 meter in length. The spreader unit is a frame rolling above the press table. The machine is designed to be easily integrated with existing press tables (delivery with new press tables is of course possible).
On the spreader unit a trolley carries the adhesive spreader and moves it perpendicular to the length of the table. In the other direction the whole machine unit moves on the table track. The adhesive is applied through the spreader across the width of the panel. Each adhesive component is pumped from an adhesive pump station positioned at the side of the production line. The pumps are air driven pistons and the mixing ratio metering is done by mechanically linked measuring cylinders.
There are two alternatives of adhesive spreaders, steel or plastic. The steel spreader has to be cleaned in a flush station after the work is complete and then the spreader may be used again. The plastic spreader will be thrown away after use.
For a one component adhesive system the spreader is automatically immersed and protected in an oil tray protecting the spreader from contact with the moisture in the surrounding air.
Operation
The operator programs the panels surface dimensions into the control system and then jogs the machine to its starting position by guiding a laser marker. When in position the operator presses the start button and the machine applies the adhesive automatically and the operator can prepare the next layer (or insert the insulation/core material) as the machine moves along the track. After the first adhesive layer is complete the process can be mirrored by turning the direction switch. When the work is complete the operator either throws away (plastic spreader) or cleans the spreader (steel spreader). After reassembling the mixer and spreader onto the machine the system is ready for use again.
Illustrations
System principal layout view 1
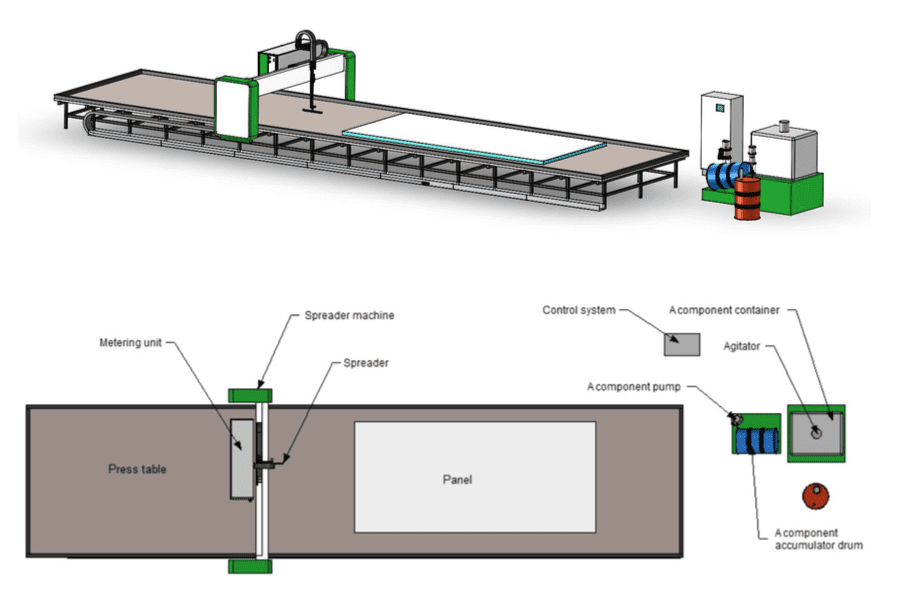
System principal layout view 2
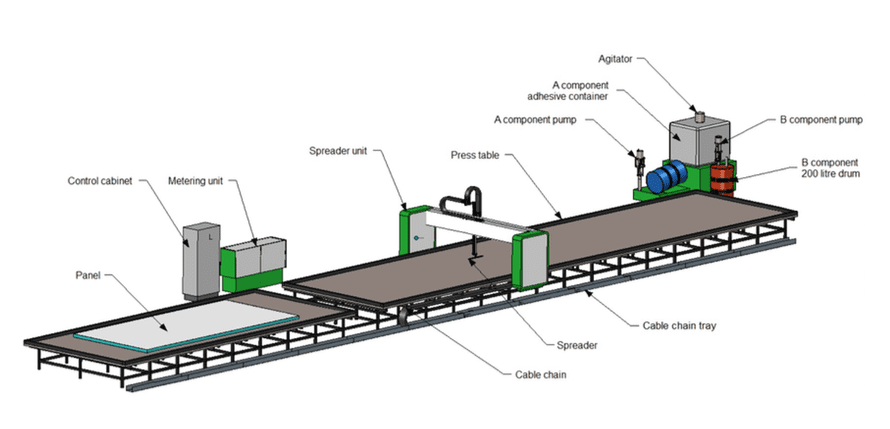
Specifications
Mixing ratio – 100:10 to 100:100 (fixed)
Metering technique – Volumetric cylinder, mechanically linked
Mixing technique – Static mixer
Capacity – Up to 8kg/min
Viscosity – Up to 100 000mPas
System pressure maximum – 270 bar
Table length – Up to 20m
Spreader width – Up to 600 mm, cc 10 mm, or 5 mm (as per request)
Nozzle outlet diameter – 1.5, 2.0, 2.5 or 3.0 mm
Machine Dimensions (LxH) – 1.0 x 2.2. Width adjusted to press table width
Net weight – 1000kg
Power electric – E: 400VAC, 3P, 50Hz, 16A
Power pneumatic – P: 6B@1000l/min
Images
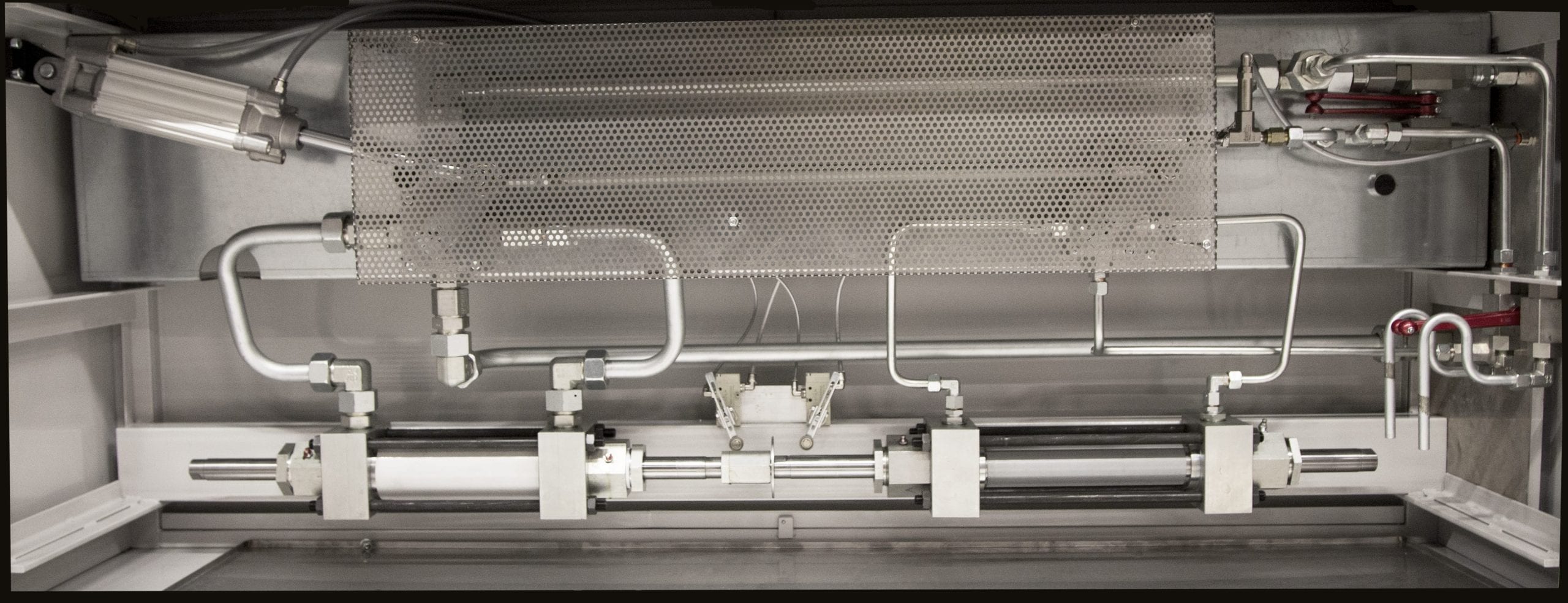
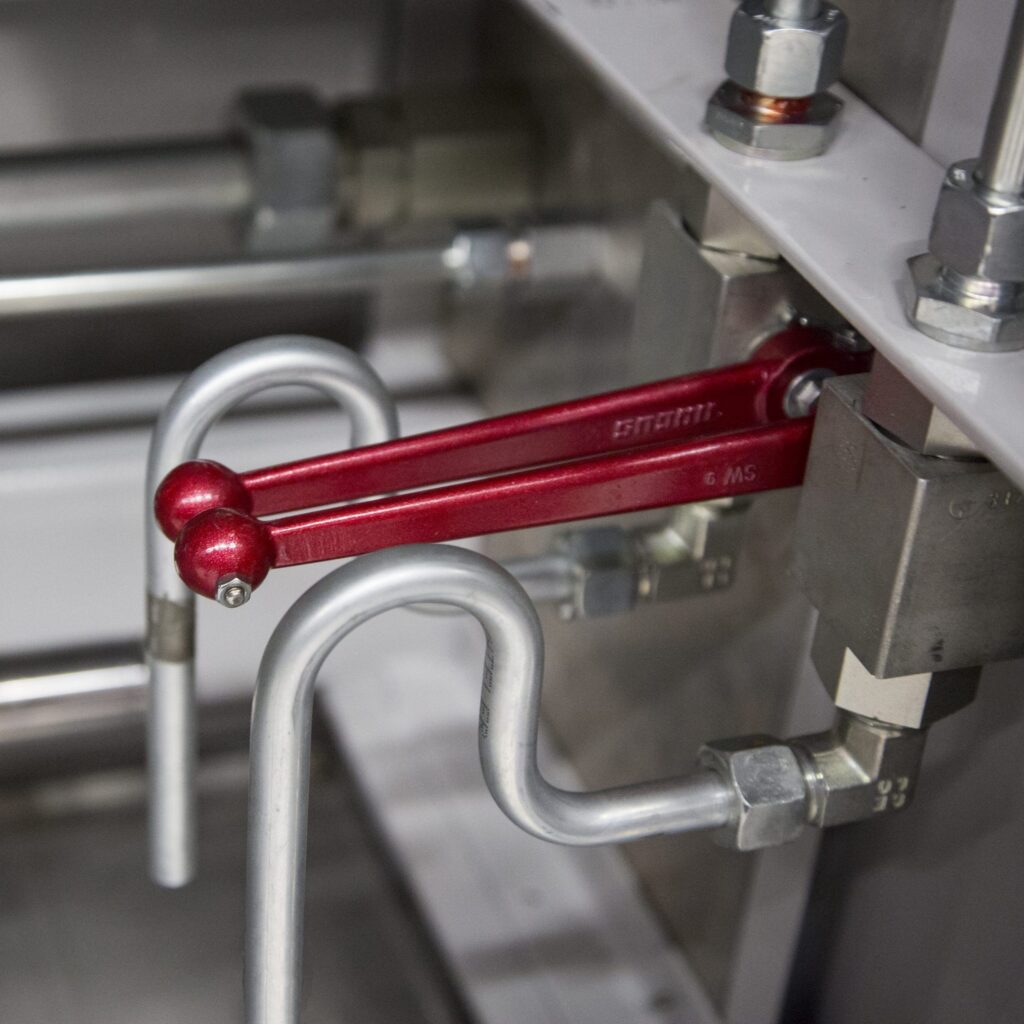
M3 – Auto
- Automatic
- 1 or 2 components
- PU, epoxy
- Small-medium panels
- Automatic measuring
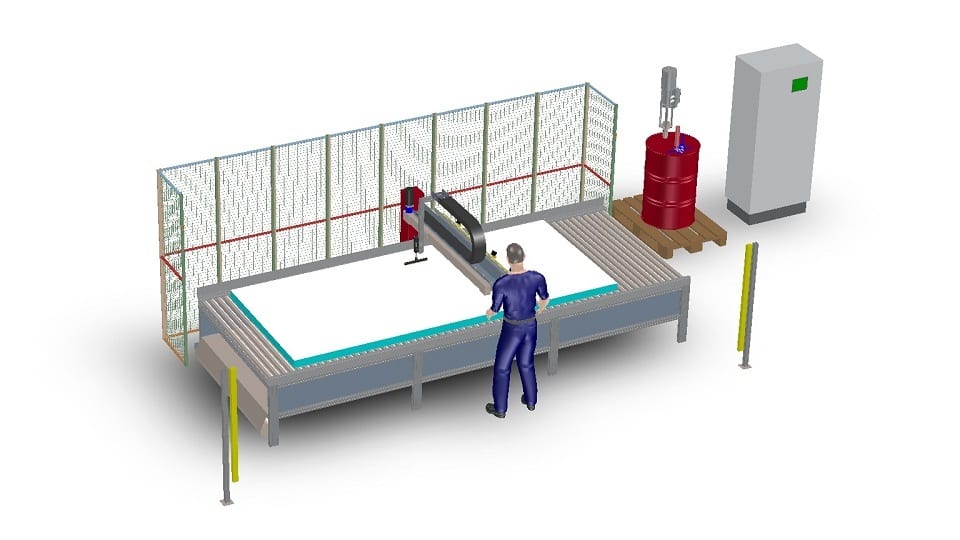
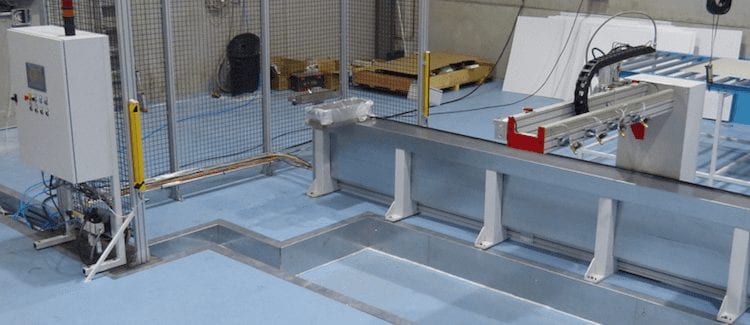
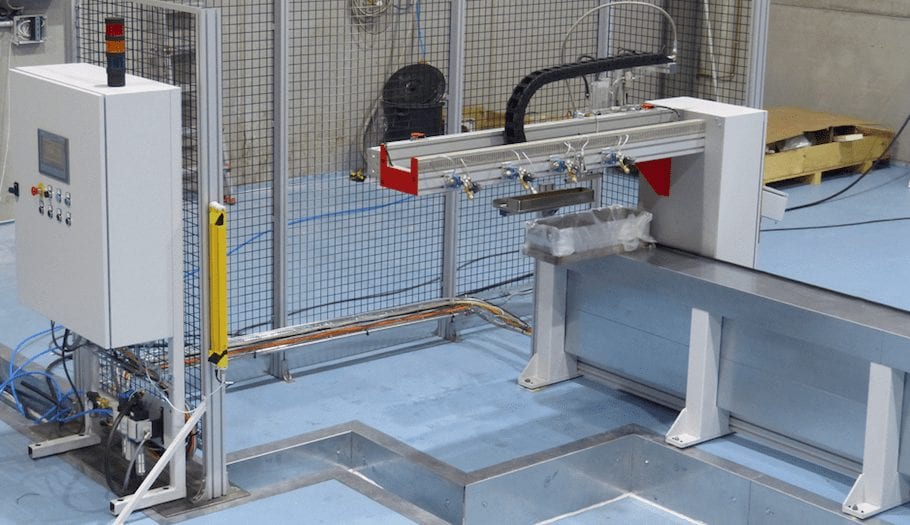
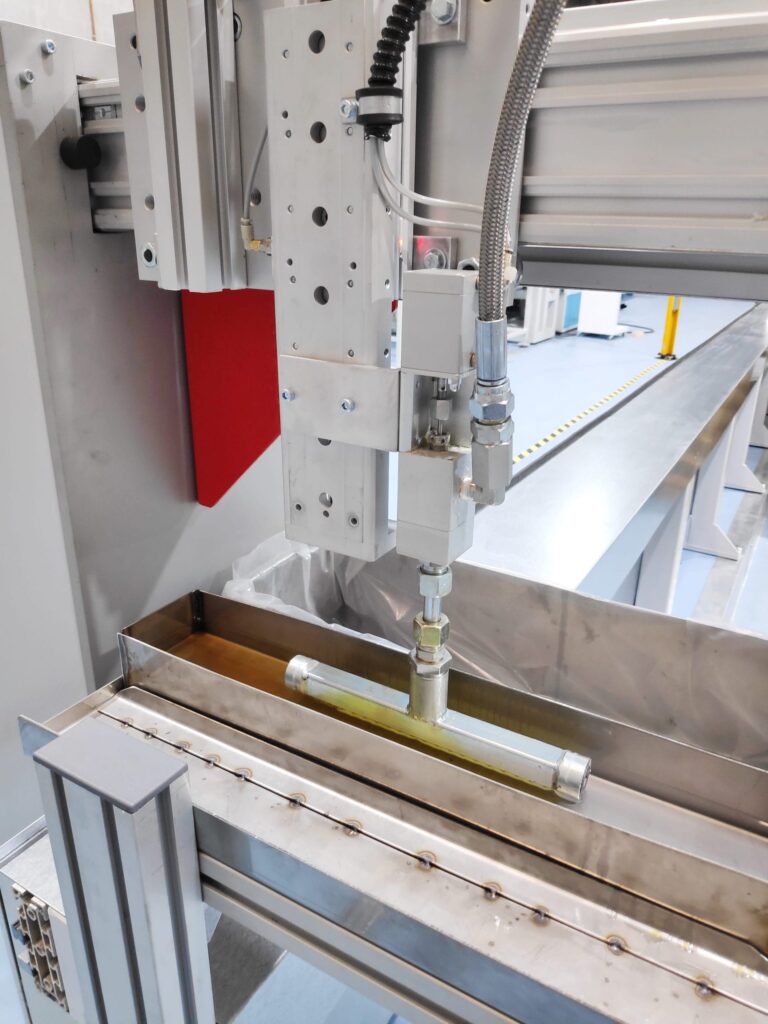
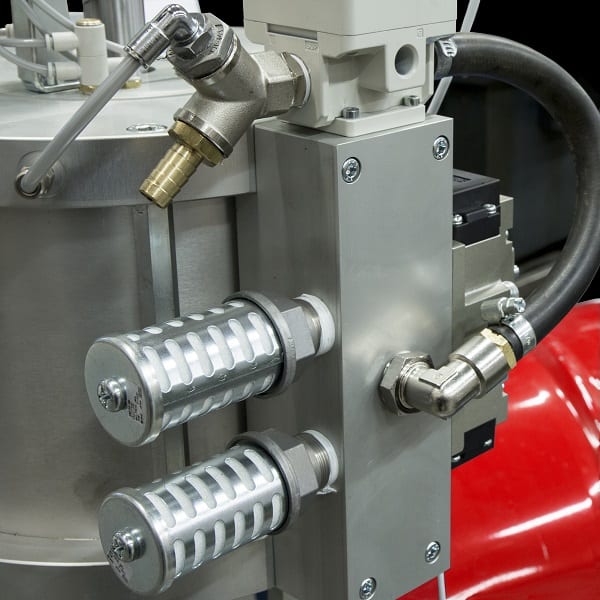
M1 & M2 – Auto
- utomatic
- 1 component
- PU
- Small-medium panels
Basic info
M2 is a classic system for pumping and spreading of one component moisture cured polyurethane. The system is specialized in manufacturing small to medium sized sandwich panels. Common areas of usage are the production of doors, mobile homes, caravans, building panels, insulation panels, facade panels or similar.
System M1 & M2 are the same with the only difference being that M1 has a fixed spreader unit and M2 a moving spreader unit.
Description
1 off automatic system for pumping and spreading of one component moisture cured polyurethane. The system will work together with a vertical lifting table where the panels are stacked. The system applies the adhesive in beads on a square surface (the panel).
The length and width of the panel is selected/programmed by the operator. Then the operator applies the core material on the working table and presses the button and the machine will start to move from its resting position to the starting edge of the panel. Now the adhesive valves are opened and the machine starts moving and the water spray is activated. Upon reaching the end side of the panel the adhesive valves are closed and the machine stops at the edge of the panel before moving to its opposite “home position”. Now when the operator presses the start button the operation will be mirrored in the opposite direction.
When the machine is at rest the nozzle protection boxes will automatically cover and protect the adhesive nozzles in order to prevent blockage.
Illustrations
M2 – moving spreader unit

M1 – fixed spreader unit
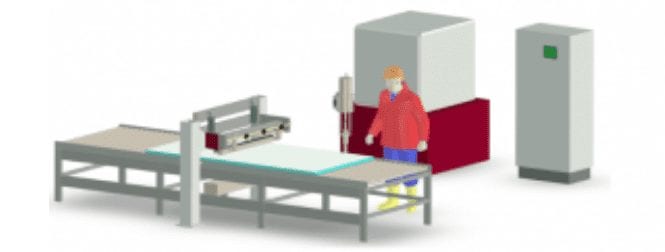
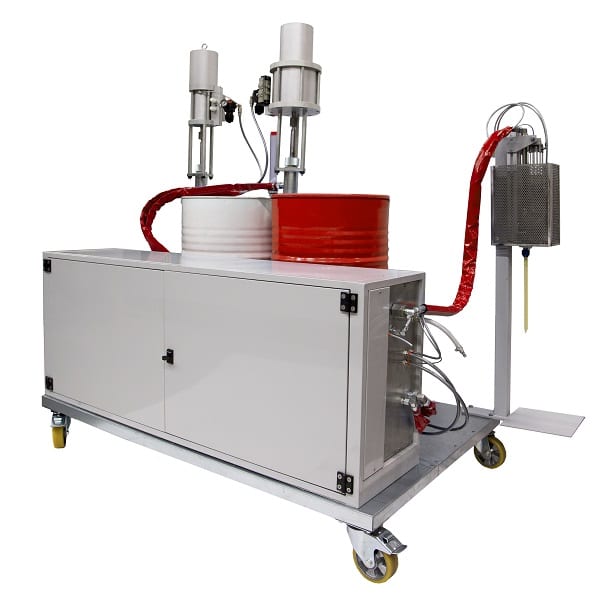
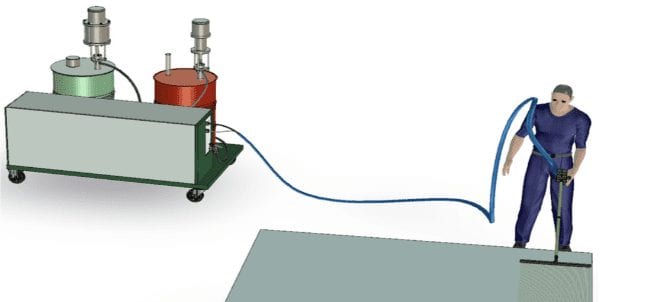
M210 – Manual
- Manual
- 2 components
- PU, epoxy, MS-polymer, wood adhesives
- Small, medium & large panels
Basic info
M210 is a manual machine system for pumping, mixing and spreading of two component adhesives customized for production and manufacturing of sandwich panels. The system serves to provide efficiency in a low quantity production of sandwich panels and can handle panels of any size.
Description
The adhesive components are pumped directly out of the 200 litre drums to the metering unit which sets the mixing ratio. The adhesive is mixed in a static mixer mounded on the outlet of the adhesive valve. The adhesive is then applied through the spreader. An extension tube between mixer and spreader allows for the operator to reach across wider panels. The metering unit together with the two adhesive drums and pumps are placed on a trolley to easily move the system around at the production site.
As a standard feature the base component is stirred through a pneumatic driven agitator to prevent sedimentation in the drum.
When the work is finished and before the adhesive is cured, the spreader, mixer and extension tube are cleaned with solvent in a flush unit to prepare them for reuse.
Illustrations
System principal layout
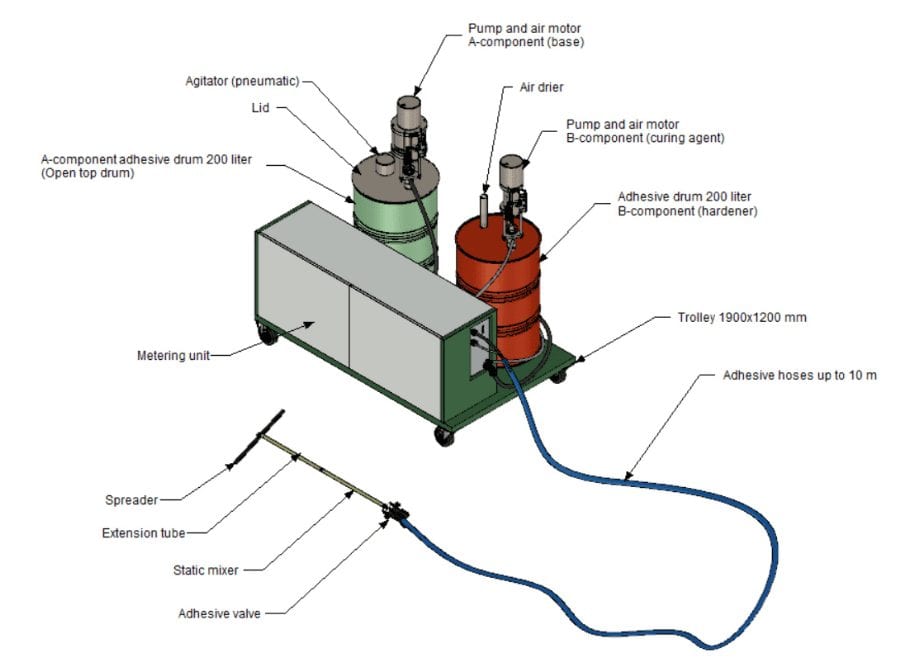
Specifications
Mixing ratio – 100:10 – 100:100 (fixed)
Metering technique – Volumetric cylinders, mechanically linked
Mixing technique – Static mixer
Capacity – Up to 6kg/min
Viscosity – Up to 100,000 mPas
System pressure maximum – 250 bar
Hose length – Up to 10m
Spreader width – Up to 600mm, cc 5 or 10mm
Nozzle outlet diameter – 1.5, 2.0, 2.5 or 3.0 mm
Dimensions LxWxH – 1.9 x 1.2 x 1.0
Net weight – 450kg
Power – 6 bar @ 1000l/min
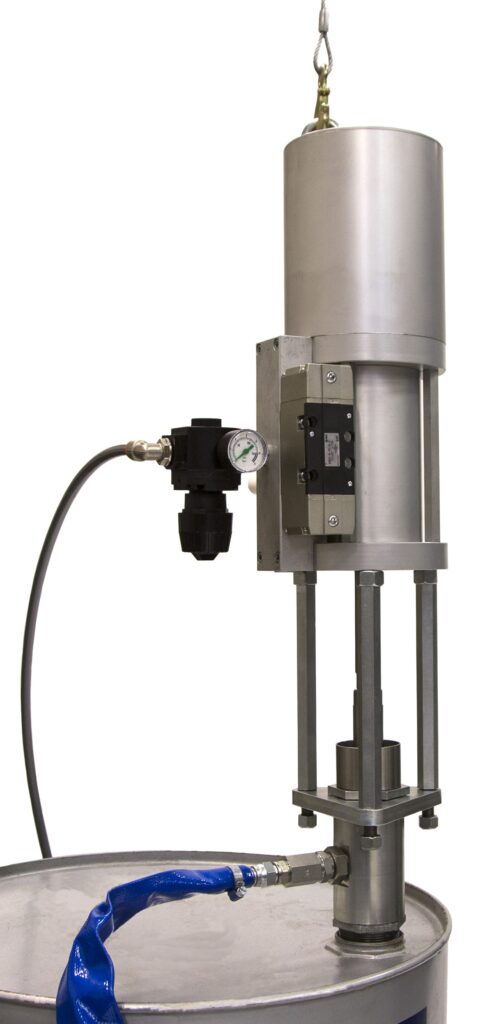
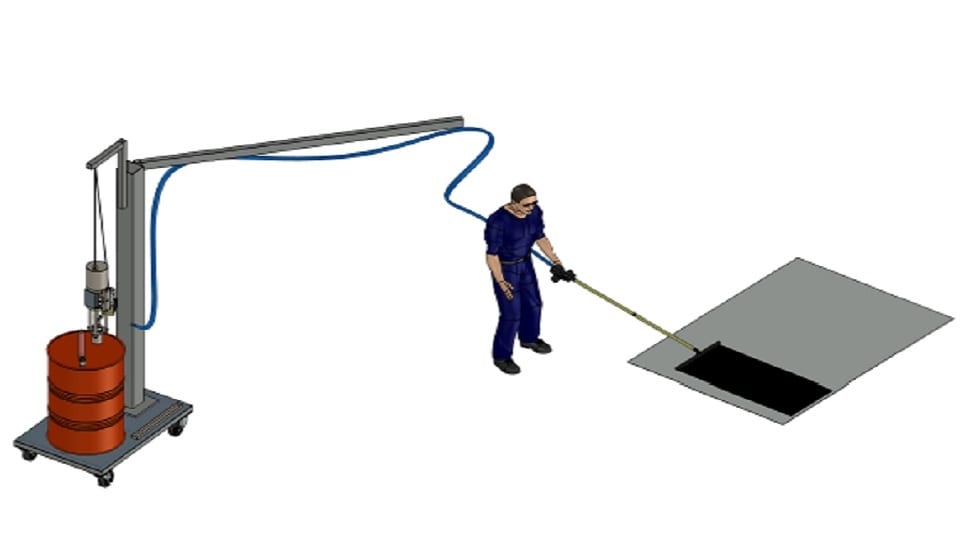
M110 – Manual
Manual
- 1 component
- PU
- Small-large panels
Basic info
The M110 is a manual machine system for spreading of one-component moisture cured polyurethane adhesive. The system serves to provide efficiency in a low quantity production of sandwich panels and can handle panels of any size.
Description
The equipment consists of a pump, a 200 liter adhesive drum, an adhesive hose, a hand-operated adhesive valve and an adhesive spreader (rake). The rake is attached to an extension tube in order to easily reach across the whole panel. The length of the hose, extension tube and spreader can be adjusted to suit the specific production conditions.When the equipment is not in use the spreader is placed in a nozzle protection box filled with inert oil to prevent the nozzle from clogging.
The equipment can be supplemented with a trolley with a jib crane to assist in the handling of the hose and in changing the adhesive drum.
Illustrations
System principal layout
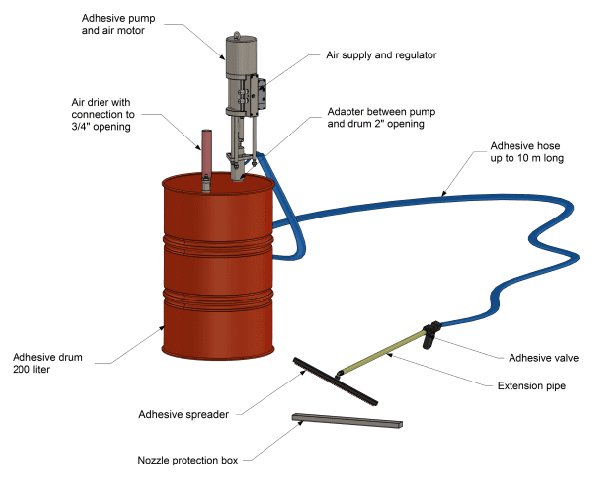
Images
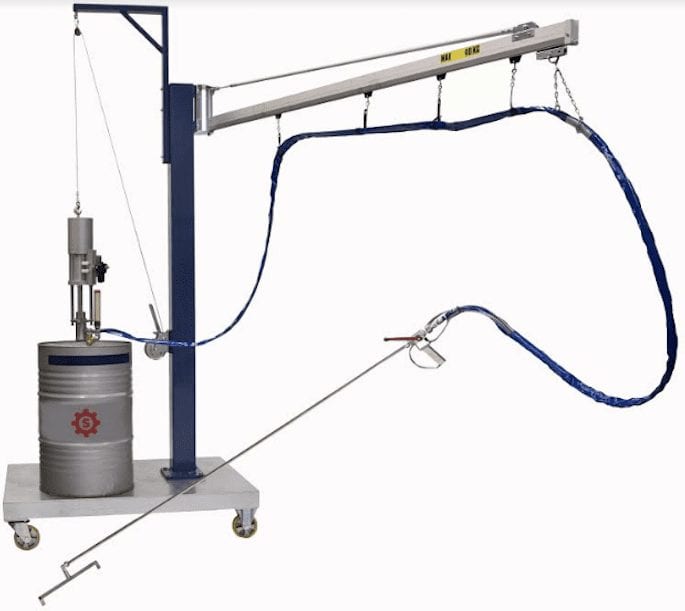
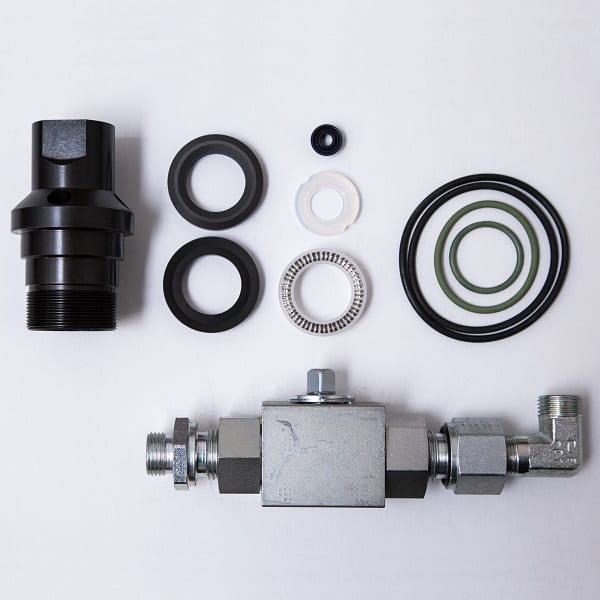
Spare parts
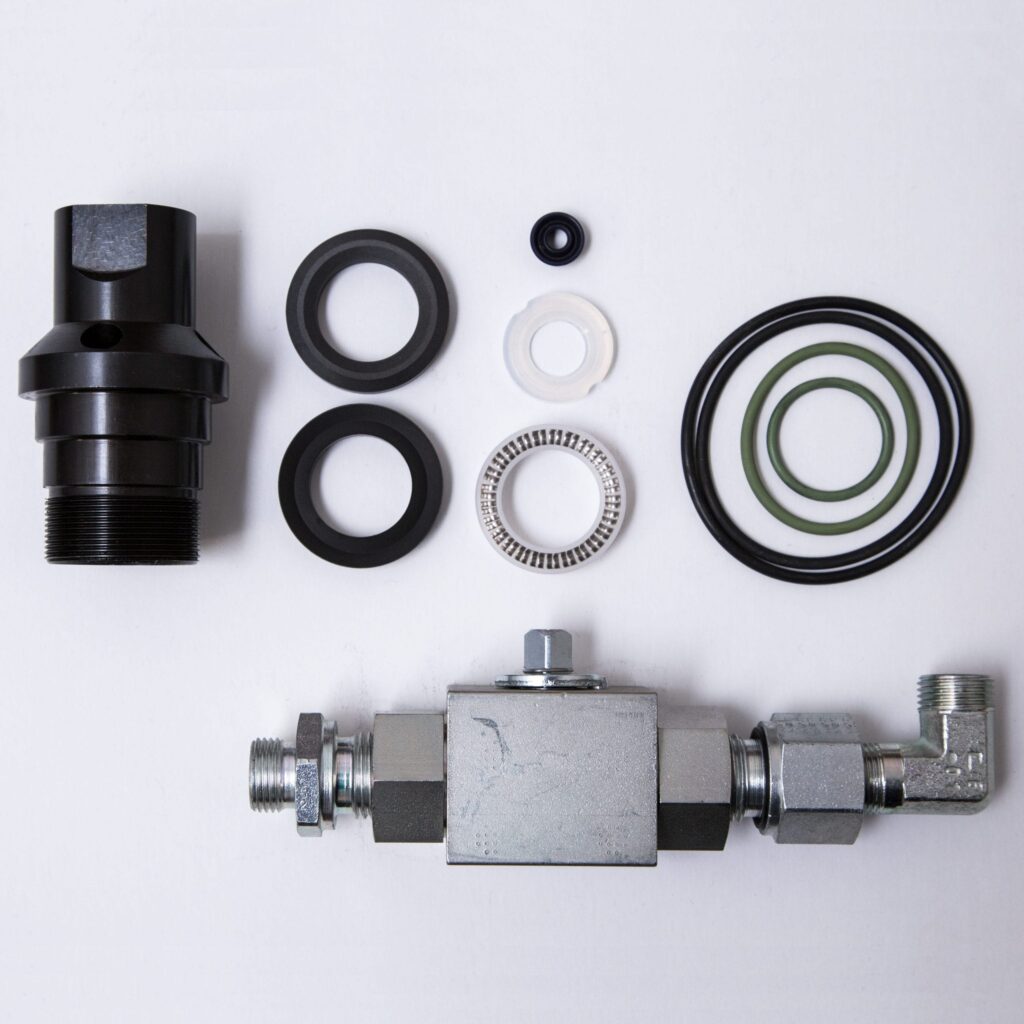
We have spare parts for most adhesive machinery. Don’t hesitate to contact us to see if we can offer you what you need.
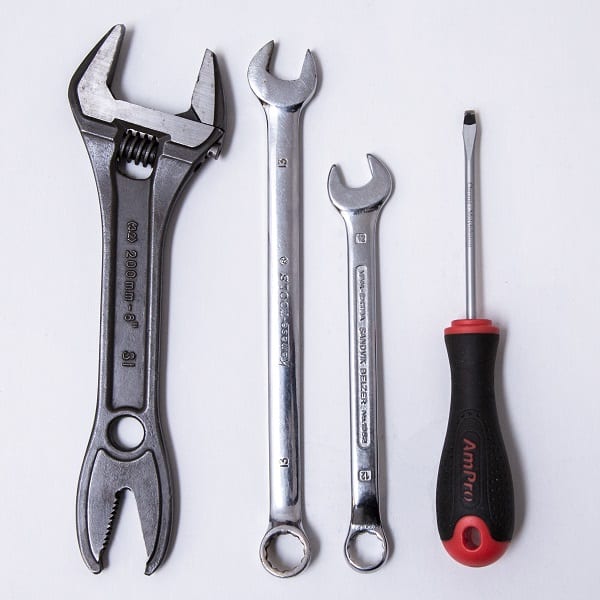
Service
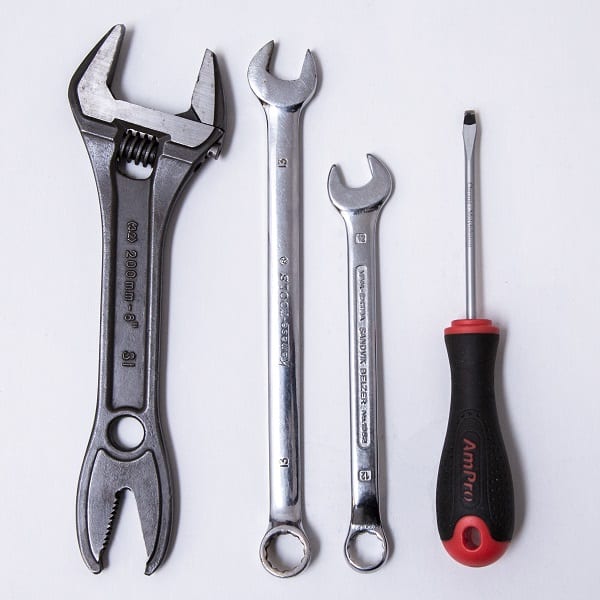
- On site service
- Self instructed self service
- Replacement & recycling of old parts
- Experience with service of most adhesive machinery
- We welcome you to contact us with any questions concerning adhesive machinery
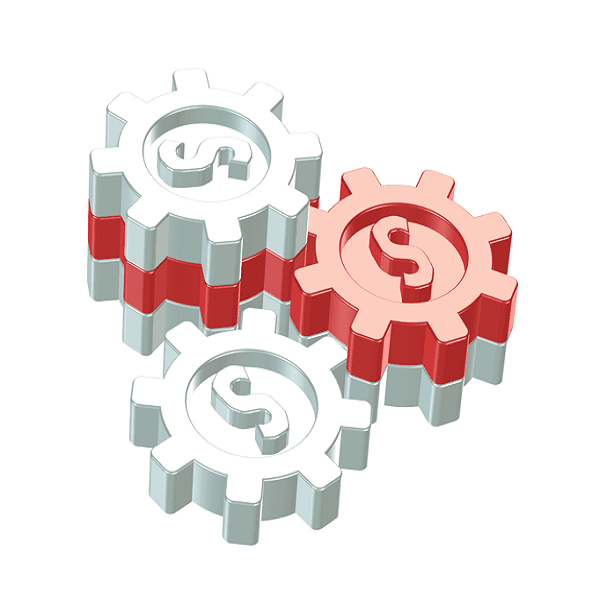
L-blocks
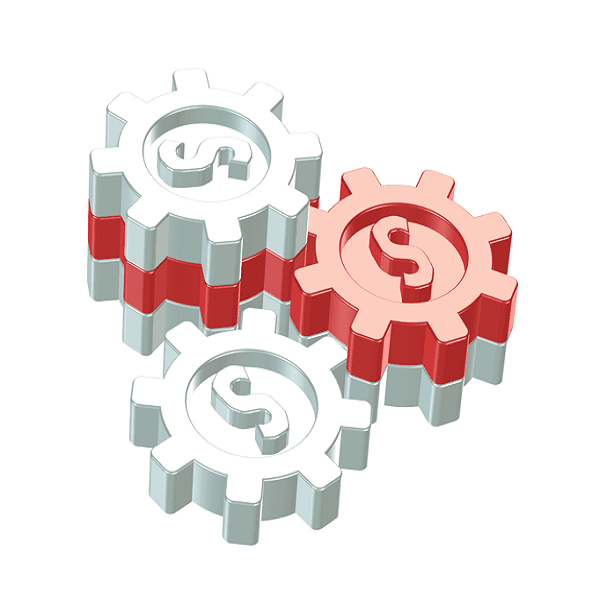
Solverk offers solutions for an efficient adhesive process. We manufacture manual and automated machines and are able to customize machine and level of automation for specific needs.
Our machines are built using a Lego block principle making it easy to expand the system, automate or update it with new technology.
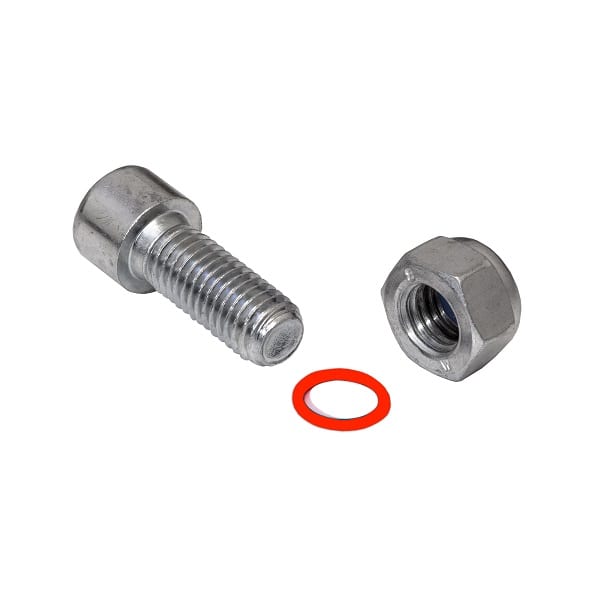
3 parts
Be part of our polyurethane three part system and increase your productivity. With a good match between us (machine builders), the adhesive supplier and you (the operator) and some team effort we think your productivity can be doubled.
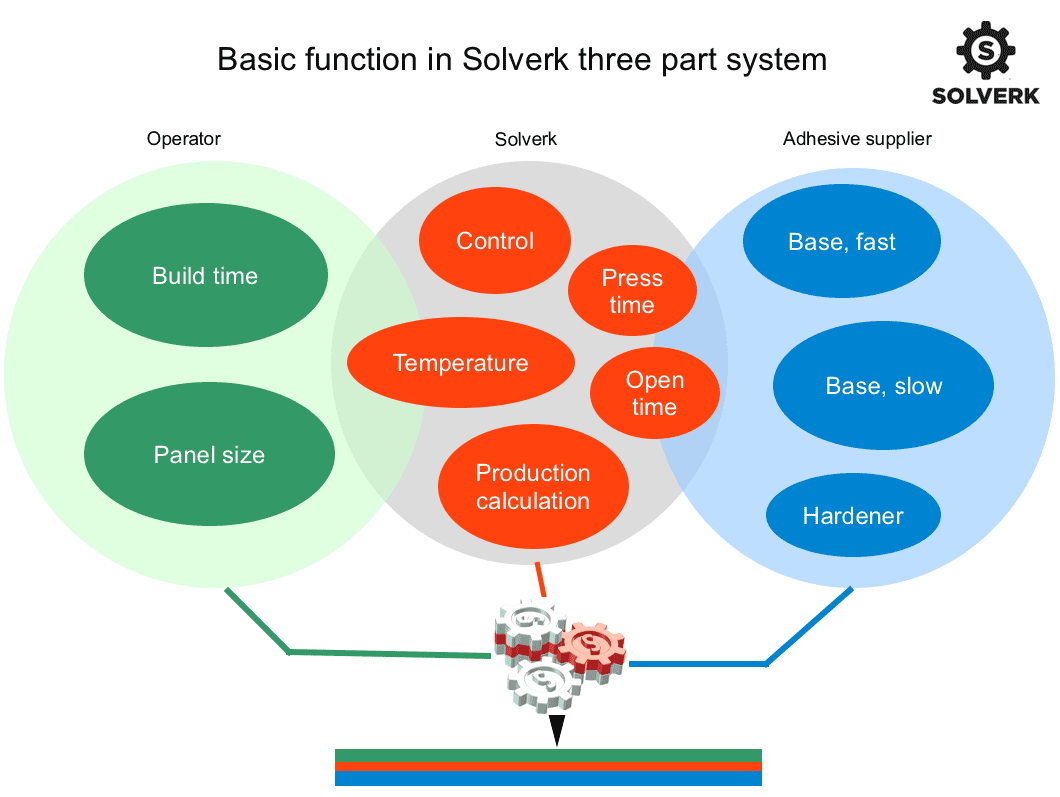
Possibilities
Optimize process time:
- Process time will always be based on first layer
Optimizing spread of adhesive mixture with respect to:
- Working/open time
- Press time
- Temperature
- Build time (panel size)
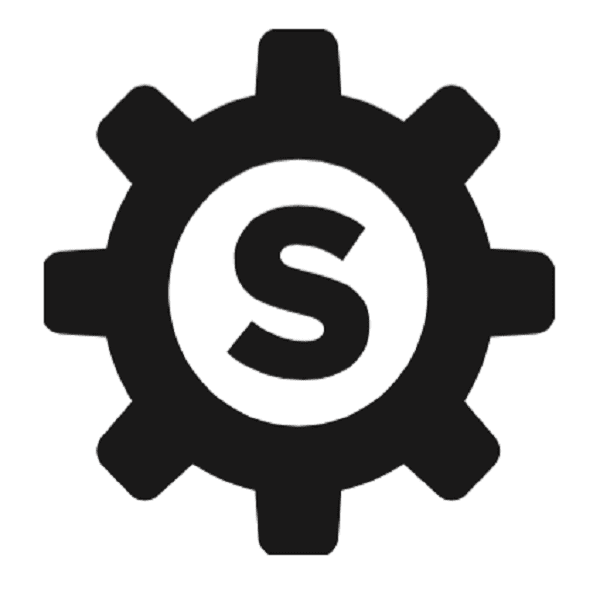
Customer list
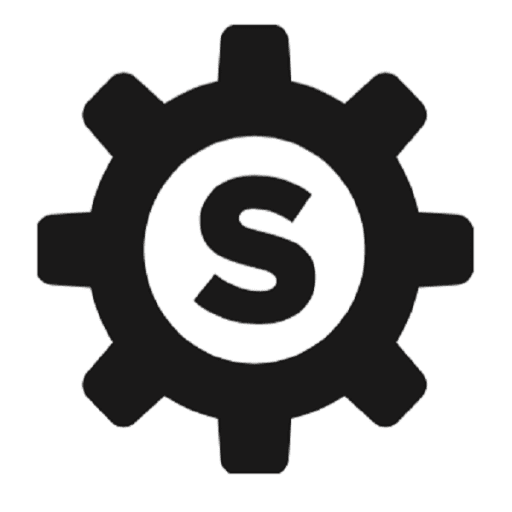
Excerpt from customer list
Akzo Nobel adhesives
Arla
Catamix SA
Dala Laminat
Daloc
Envi-Filter AS
Jackon AS
KABE husvagnar
Kenpo sandwich
KTH
Lindab
Nordfarbo
Norfrig
PLS truck bodies
Risenta
Rockingham Systems LTD
Senseair
SIKA
Scania
Tetra pak
Thermoeurop SPA
Trigano SPA
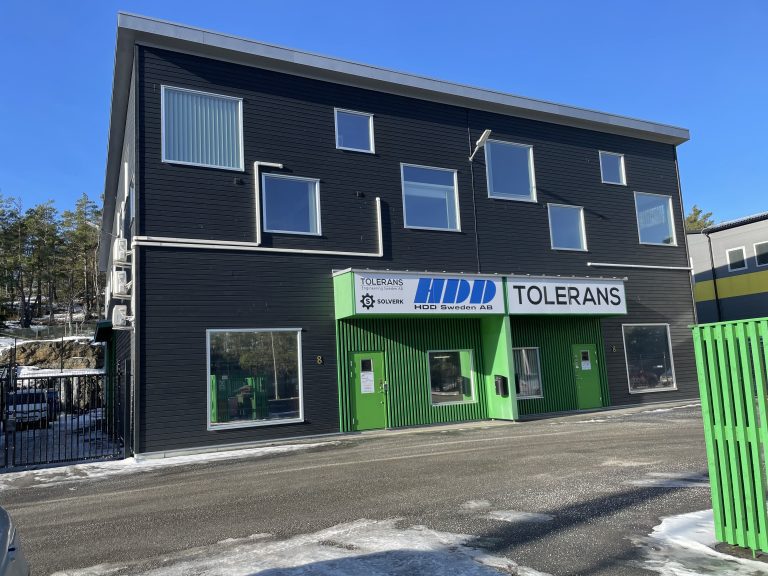
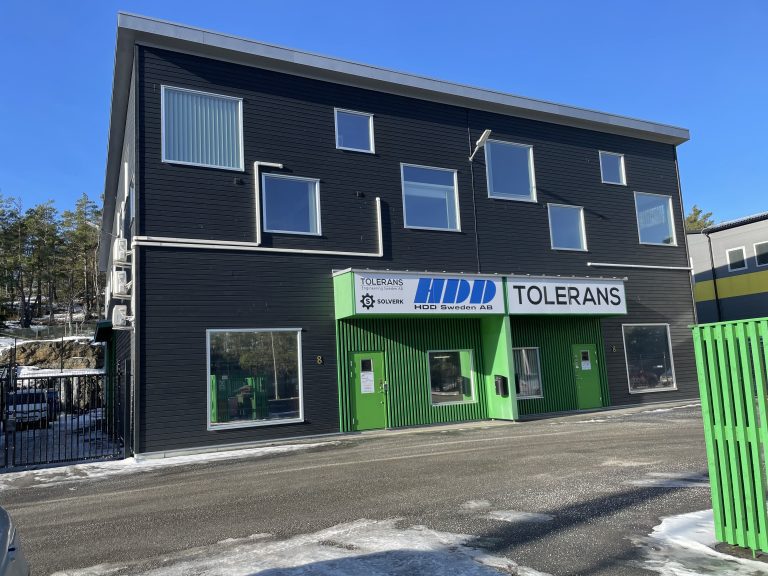
Contact
Solverk Systems AB
Grustagsvägen 8
138 40 Älta
Sweden
Info@Solverk.se
Tel: +46 8 35 50 60
Org. nr: 556770-7038
Bankgiro: 5668-5571
VAT: SE556770-703801
BIC/SWIFT: HANDSESS
IBAN: SE2760 0000 0000 0923 2419 81
About
The core of Solverk Systems is our engineering and mechanic skills with our staff having worked with the development of adhesive machines and improvement of adhesive processes for over 15 years. Solverk Systems aims to be a leader in the development of adhesive machines and offer reliable and easy to implement solutions.
SOLVERK AB +46 8 35 50 60 info@solverk.se